SUPERIOR SURFACE PREPARATION — AUTOMATED
GRIT BLASTING MACHINE
WHAT IS AUTOMATED GRIT BLASTING?
Automated grit blasting uses robotic systems or machines to precisely apply abrasive materials to parts, creating a consistent surface texture for coating adhesion or cleaning. This process is faster, more efficient, and ensures uniform results compared to manual blasting, making it ideal for high-volume production. Automated systems also reduce operator fatigue and improve safety by controlling the blasting environment.
-
Benefits of Automated Grit Blasting
Consistency: Ensures uniform surface texture across all parts.
Efficiency: Speeds up the blasting process, increasing throughput for high-volume production.
Precision: Provides controlled, accurate application of abrasives for optimal results.
Safety: Reduces operator exposure to hazardous materials and dust.
Reduced Labor: Decreases the need for manual labor, lowering operational costs.
Scalability: Easily scalable for large production runs, maintaining quality and consistency.
-
1. Part Loading: Parts are loaded into the automated blasting machine, often using conveyors or robotic arms.
2. Abrasive Selection: The system selects the appropriate abrasive media (e.g., aluminum oxide, glass beads) for the job.
3. Blasting: High-pressure air or centrifugal force directs the abrasive media onto the part's surface to remove contaminants or create texture.
4. Cleaning: After blasting, the parts are typically cleaned to remove any residual abrasives.
5. Part Unloading: Once the blasting is complete, parts are unloaded and ready for further finishing or coating processes.
-
Aerospace:
- Turbine blades, brackets, and other critical components
- Prepares parts for coating adhesion and surface cleaning
Automotive:
- Engine blocks, pistons, and wheels
- Removes contaminants and creates textured surfaces for coating
Firearms:
- Uppers, lowers, and receivers
- Ensures optimal surface texture for coatings like Cerakote
Medical:
- Surgical tools, implants, and medical devices
- Cleans and textures surfaces for coating adhesion and biocompatibility
Military/Defense:
- Firearm components, tactical equipment
- Surface preparation for coatings and corrosion resistance
SOLUTIONS ENGINEERED FOR PRECISION
SOLUTIONS ENGINEERED FOR PRECISION
SOLUTIONS ENGINEERED FOR PRECISION SOLUTIONS ENGINEERED FOR PRECISION
Which Blasting Method is Right For Me?
Grit blasting uses angular abrasives to create a rougher surface profile, ideal for promoting coating adhesion or removing tough contaminants.
In contrast, Shot Blasting with steel or stainless steel shot creates a smoother, peened surface, which is better for stress relief, surface strengthening, or achieving a polished finish.
The choice depends on whether the goal is preparation for coating (grit blasting) or enhancing durability and surface finish (shot blasting).
How Grit Blasting Benefits Aluminum Anodizing
Grit blasting uses angular abrasives to prepare aluminum surfaces, creating a consistent texture that enhances the adhesion and durability of Type II and Type III Anodized coatings.
For Type II Anodizing, it ensures a uniform finish, ideal for decorative applications, while for
Type III Hardcoat Anodizing, it optimizes surface roughness to achieve maximum hardness and wear resistance.
This preparation step removes contaminants and smooths surface irregularities, providing a clean foundation for superior anodizing results.
How Grit Blasting Benefits Cerakote Applications
Grit blasting uses angular abrasives to create a textured surface, ensuring optimal adhesion of Cerakote coatings.
This process removes oils, oxidation, and other contaminants, providing a clean foundation that enhances coating durability, corrosion resistance, and overall performance.
The uniform surface profile created by grit blasting is essential for achieving Cerakote's signature smooth, long-lasting finish
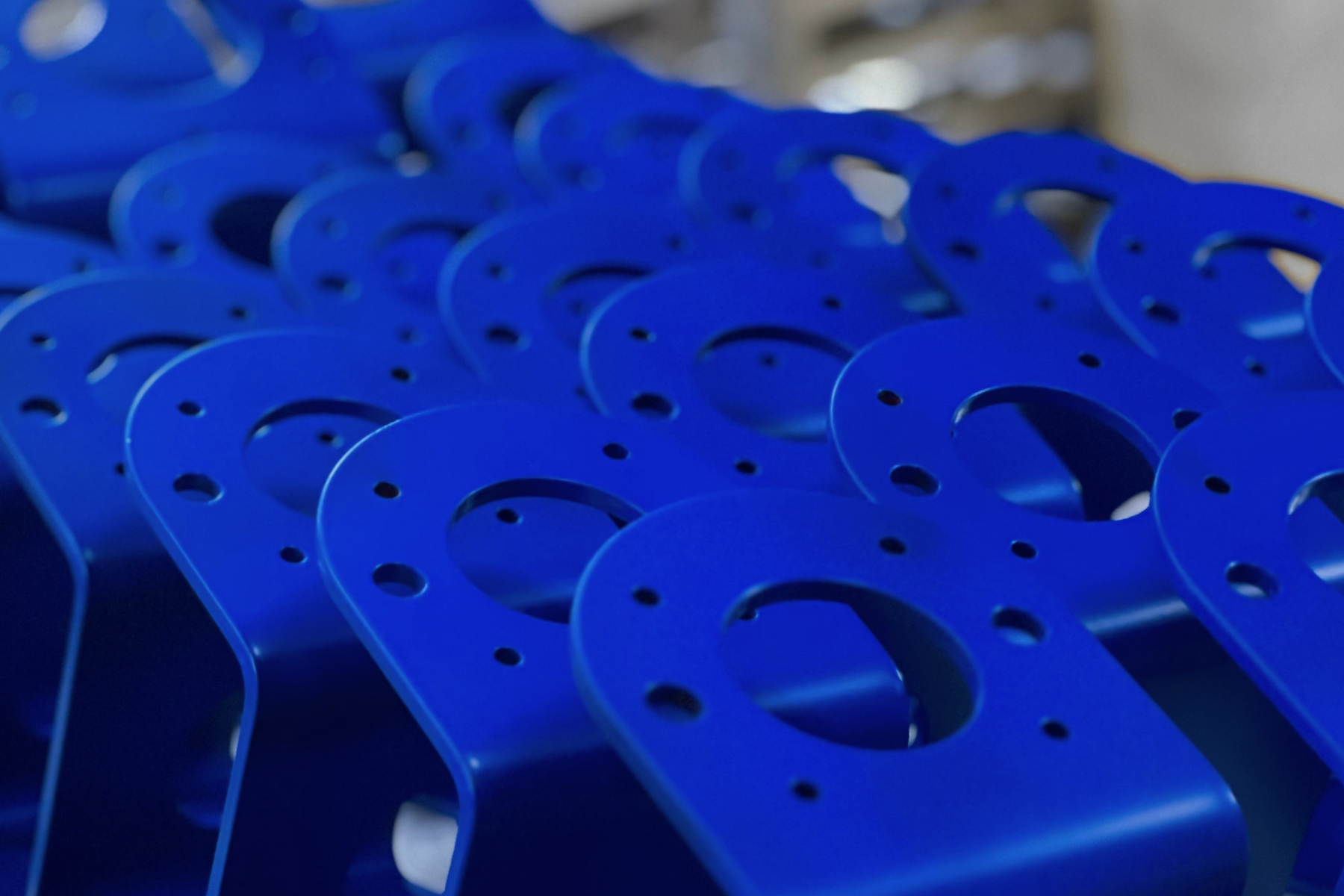
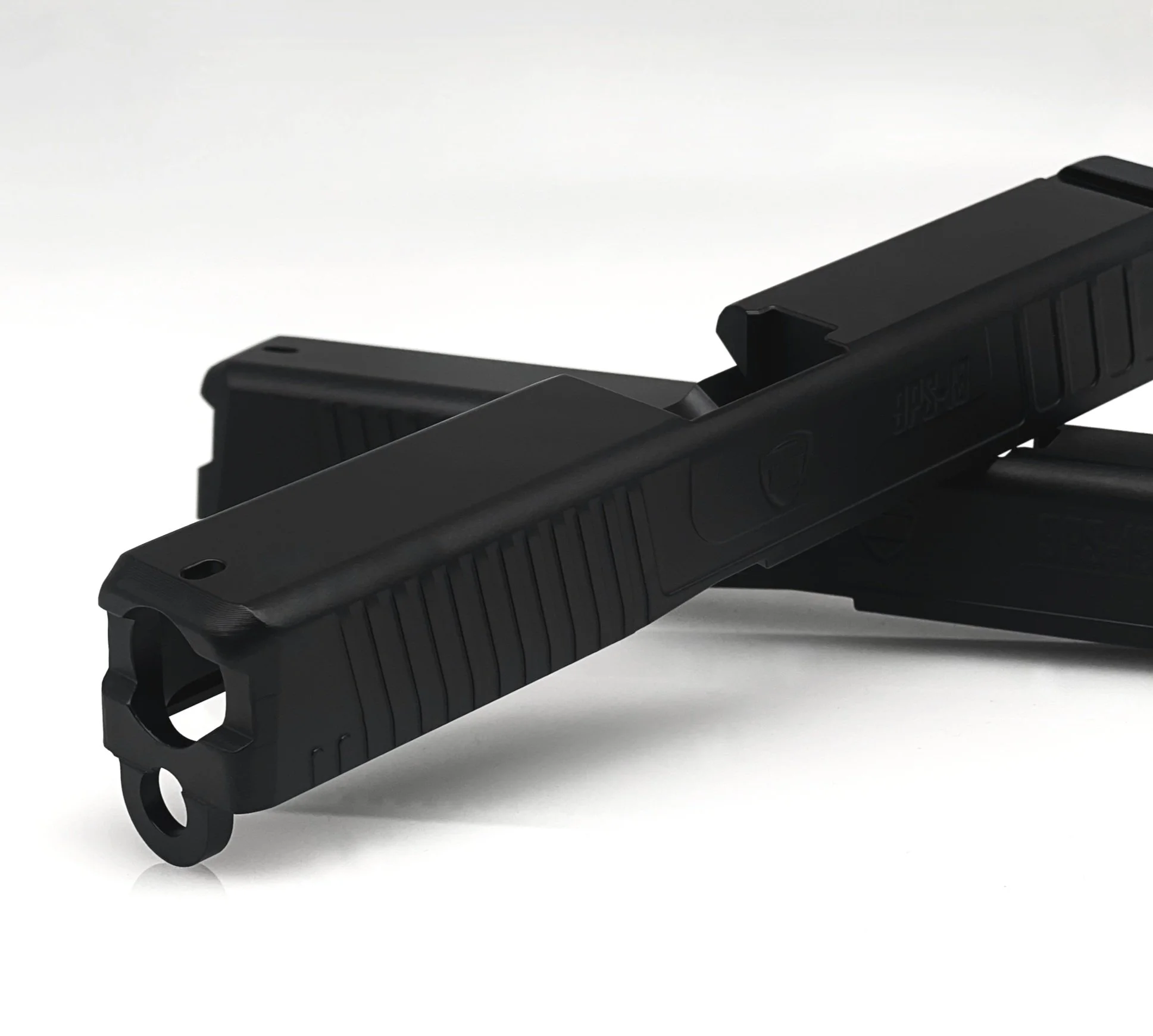




