PRECISION HARDCOAT ALUMINUM ANODIZING - TYPE 3
What Is Hardcoat Anodizing?
Hardcoat aluminum anodizing is a thick, wear-resistant anodic layer that enhances aluminum’s durability, corrosion resistance, and hardness. Ideal for demanding applications, it provides superior protection against abrasion and extreme environments, significantly extending the lifespan of aluminum components.
We apply colored dyes after aluminum anodizing. The parts undergo sealing to reduce color fading.
Class 1 and 2; MIL-A-8625 and MIL-PRF-8625 for Type 2 and Type 3 Aluminum Anodizing.
Type 2 Coating Thickness: .0001 to .001 mil
Type 3 Coating Thickness: .0008 to .002 mil
Current Lead time: 3-5 days
Black
O.d. Green
Dark O.D. Green
Dark Grey
Grey
Dark Tan
Tan
Hardcoat Clear
Benefits of Type 3
-
Type III anodizing creates a significantly thicker and denser oxide layer compared to Type II, resulting in enhanced durability and wear resistance. This hard coat provides exceptional protection against mechanical damage, such as abrasion and impact, making it ideal for heavy-duty applications, including industrial machinery and aerospace components. The increased thickness of the oxide layer contributes to a surface hardness similar to that of case-hardened steel.
Type III anodized surfaces are particularly well-suited for applications requiring extreme wear resistance, such as military or defense equipment. The surface can withstand repeated mechanical stress without significant wear, making it ideal for parts that experience friction and movement. -
The oxide layer in Type III anodizing typically features fewer open pores compared to Type II, creating a more sealed surface that enhances its protective properties. This closed-pore structure boosts resistance to chemicals and prevents moisture and other substances from infiltrating the surface, ensuring superior long-term protection in corrosive environments.
-
During the hard anodizing process, careful control of the process parameters helps eliminate surface contaminants and residue, creating a cleaner and more stable finish. This feature is particularly beneficial in precision engineering applications where even slight residue could affect the function or integrity of parts.
-
The dense, hard surface layer formed during Type III anodizing resists the adhesion of dirt, oil, and other contaminants, making the surface easier to clean and maintain. This quality is essential in environments where cleanliness and hygiene are critical, such as in food processing or medical equipment.
-
The increased thickness and density of the anodized layer in Type III processes help lock in dyes more effectively, reducing the fading that can occur over time due to exposure to UV light or harsh environmental conditions. This characteristic ensures that colored parts maintain their vibrant appearance longer, even under demanding conditions.
-
Despite its thickness, the anodized coating in Type III anodizing maintains a high level of thermal conductivity. This makes hardcoat anodized aluminum suitable for components that need effective heat dissipation, such as heat sinks in electronic devices or engine parts.
-
The hard anodized layer often exhibits a lower coefficient of friction, which can enhance the performance of moving parts by reducing wear and improving efficiency. This characteristic is beneficial in machinery where parts slide or rotate against each other.
-
When left unsealed, the anodized layer formed by Type III anodizing has enhanced water-resistant properties, making it suitable for applications that involve prolonged exposure to moisture. This unsealed state allows the oxide layer to remain porous enough to retain its hydrophobic qualities without the need for additional coatings.
-
Unsealed Type III anodized surfaces offer excellent adhesion properties for paints, sealants, and other coatings. The porous nature of the unsealed surface allows these secondary treatments to anchor firmly, resulting in better bonding and improved overall durability of the applied coatings.
Black
Clear
Grey
O.D. Green
Red
Purple
Tan
Blue
S.D. Green
Green
Copper
Gold
Orange
Colors shown are for general reference only. Other colors may be available upon request.
Shot blasting uses high-speed abrasive blasts to clean and prepare surfaces, enhancing adhesion and durability. Automation ensures consistent, efficient surface preparation, ideal for removing rust, scale, or contaminants from metal parts.
We recommend Shot Blasting as a preparation prior Anodizing to remove contaminants and ensure a consistent, high-quality, and uniform finish for better protection and performance.
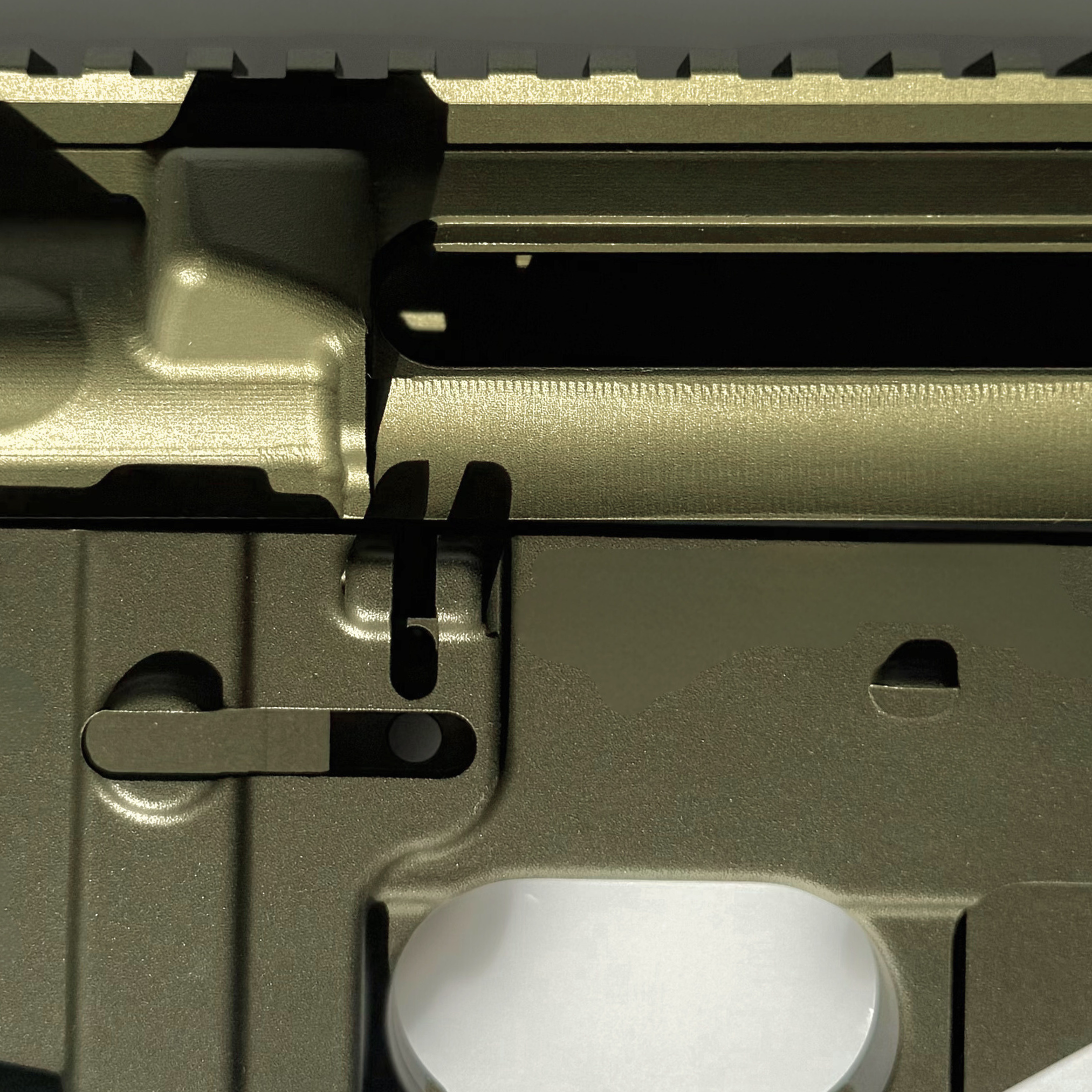
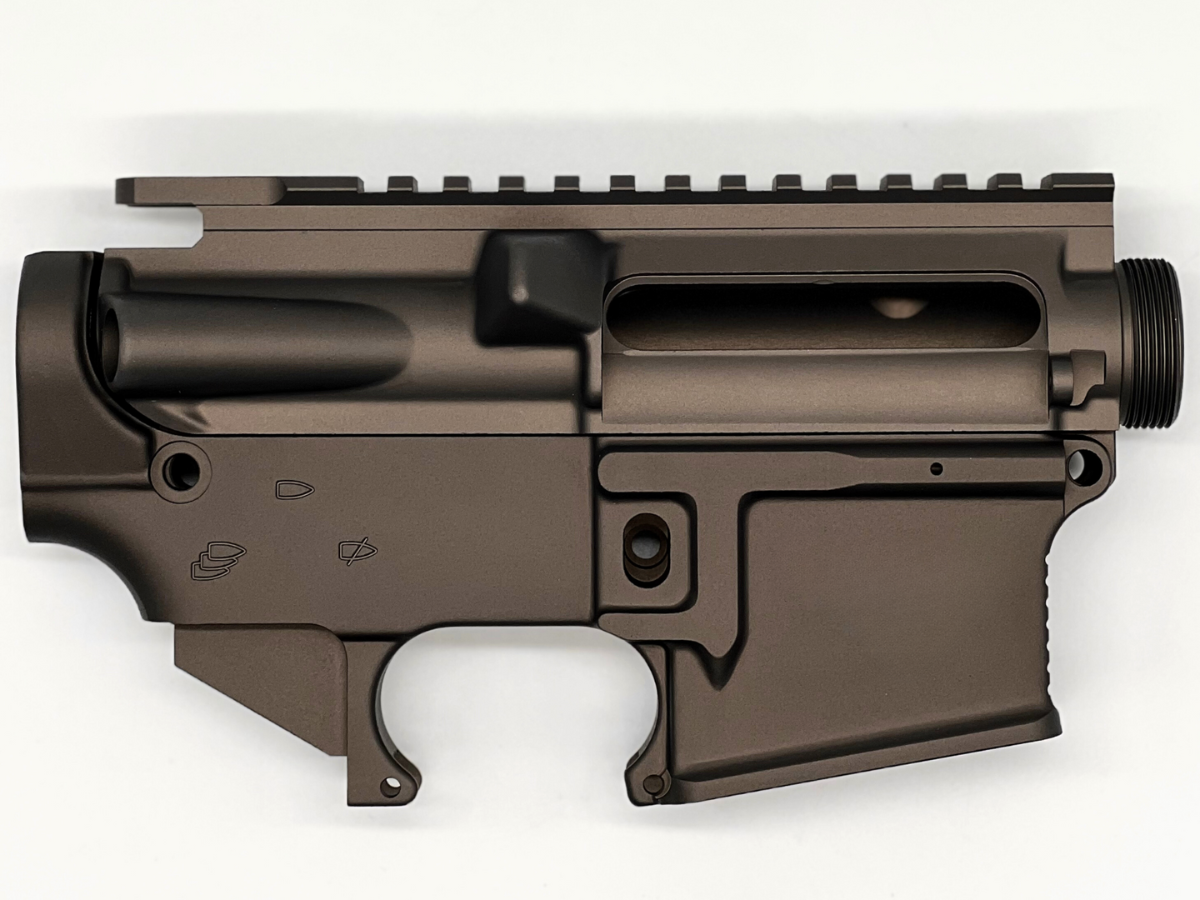







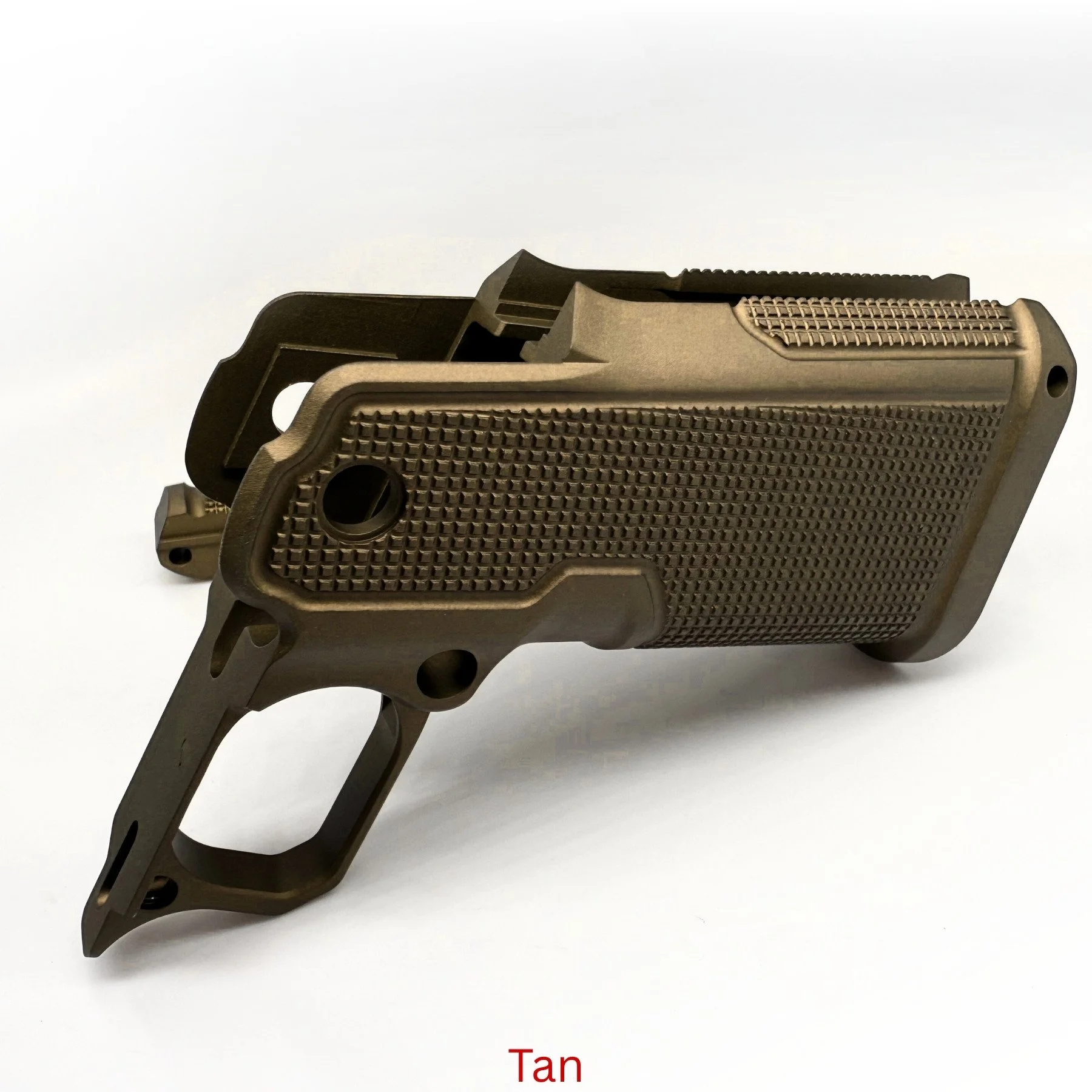
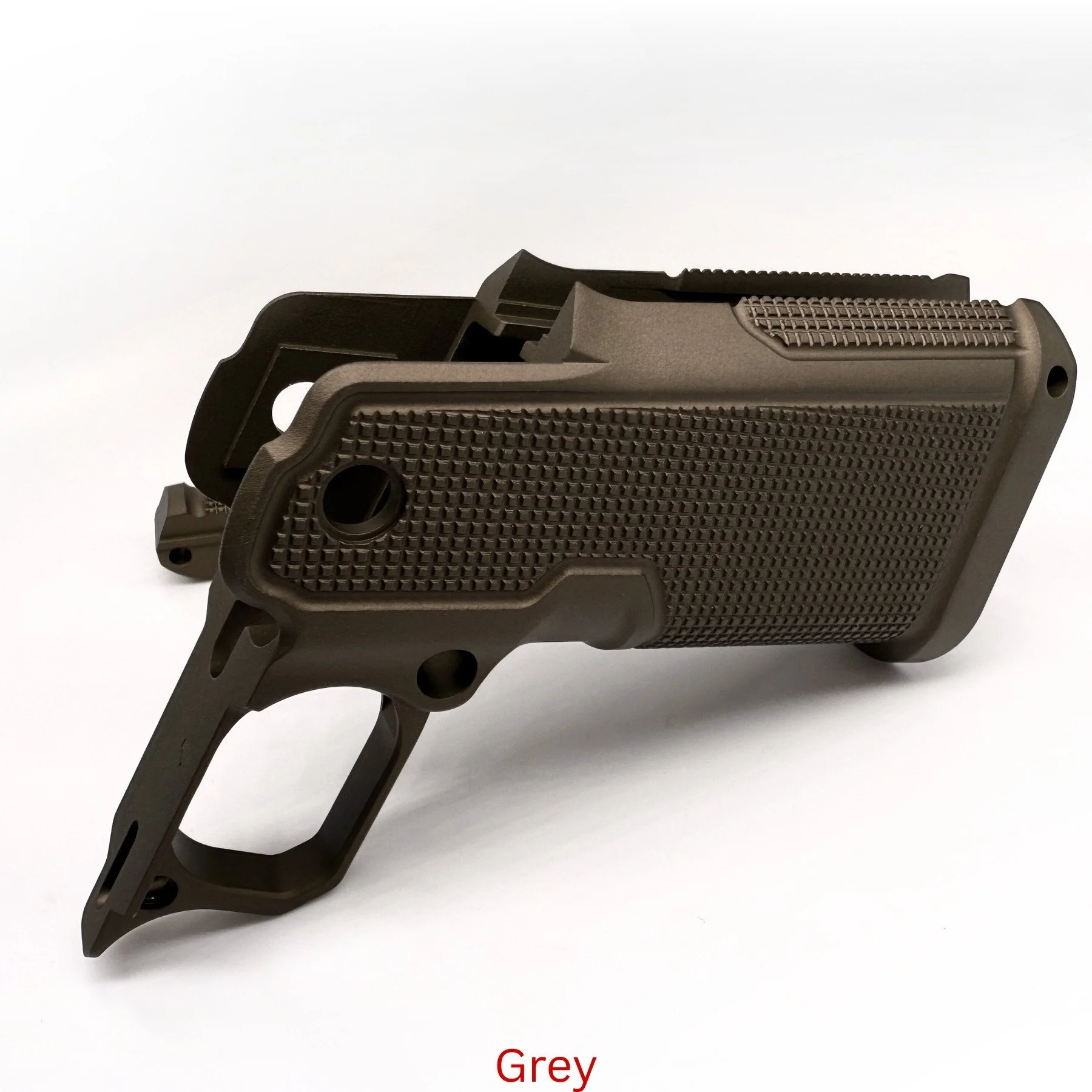


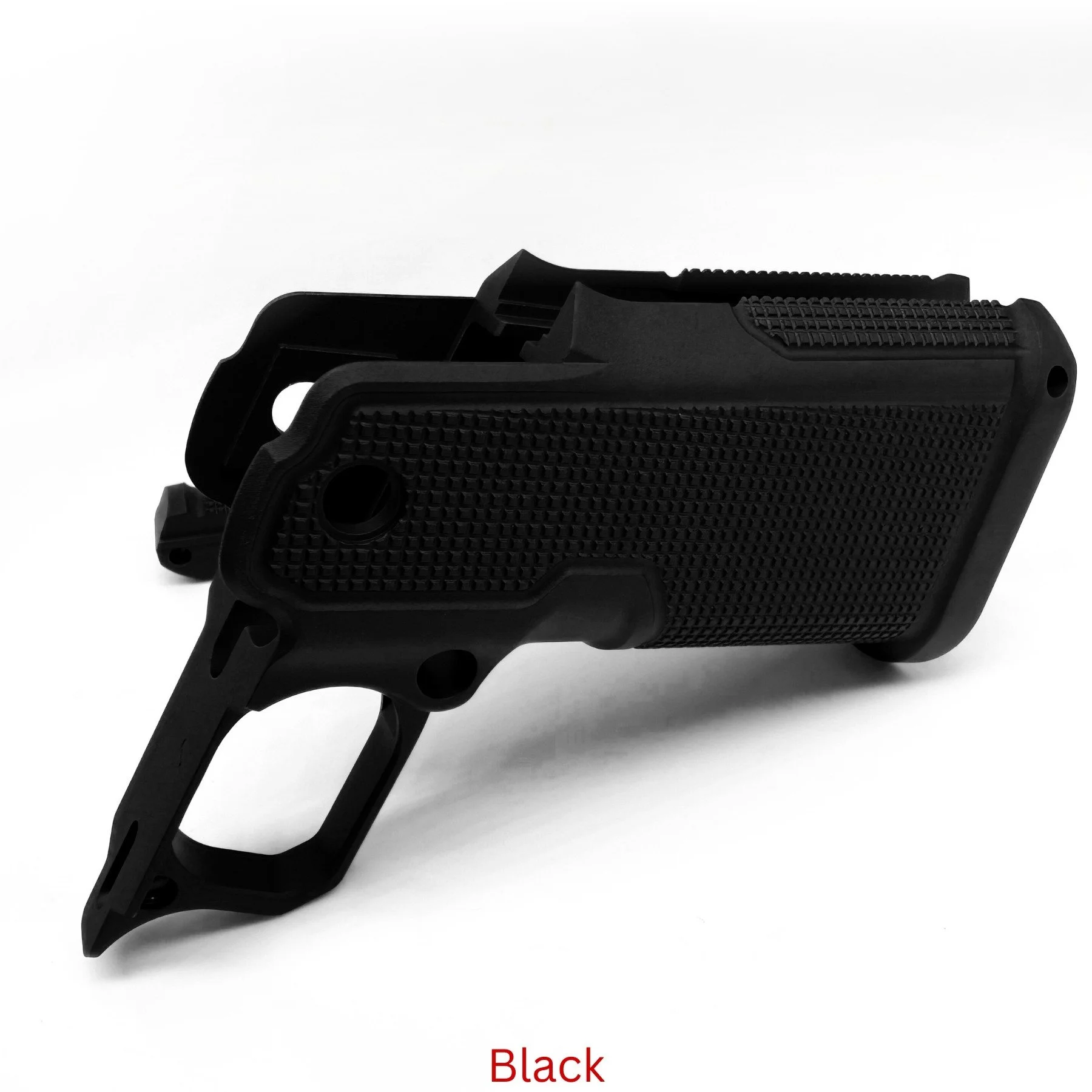
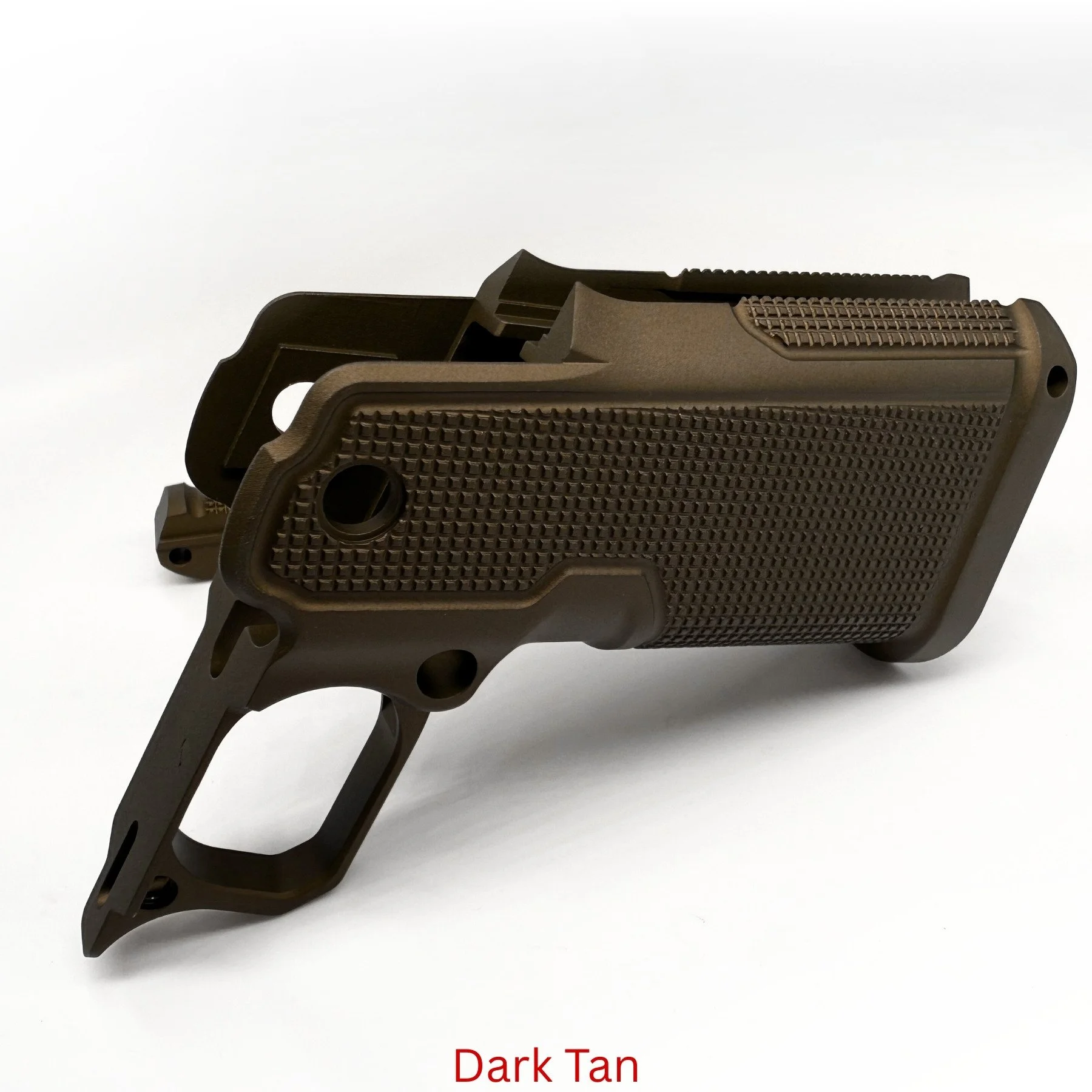
