ELECTROPOLISHING —
SUPERIOR SURFACE FINISHING
WHAT IS ELECTROPOLISHING?
Electropolishing is a metal finishing process that uses an electrochemical reaction to remove a thin layer of material from the surface of a metal part, smoothing and polishing it to create a bright, reflective finish.
Often referred to as “reverse plating,” electropolishing involves submerging the metal part in an electrolytic solution and applying a current. This selectively dissolves the rough or high points on the metal surface, leaving a smooth, uniform finish.
-
The electropolishing process, also known as electrochemical polishing, dissolves surface imperfections down to the micron, leaving the surface clean and polished. We carefully formulate our electrolyte chemistries to ensure optimum results for stainless steel finishing.
-
Up to 30x corrosion resistance over passivation
No directional lines from abrasive polishing
Strips contaminants
Smooths surface imperfections
Uniform Luster
Meets tight tolerances
I.D. Polishing
-
Medical implants and devices
Surgical instruments
Aerospace components
Precision electronic components
Light fittings
Cookware and utensils
Hydraulic fittings
Fasteners
Wire racks
Automotive parts
-
Aerospace
Automotive
Medical
Pharmaceutical
And More!


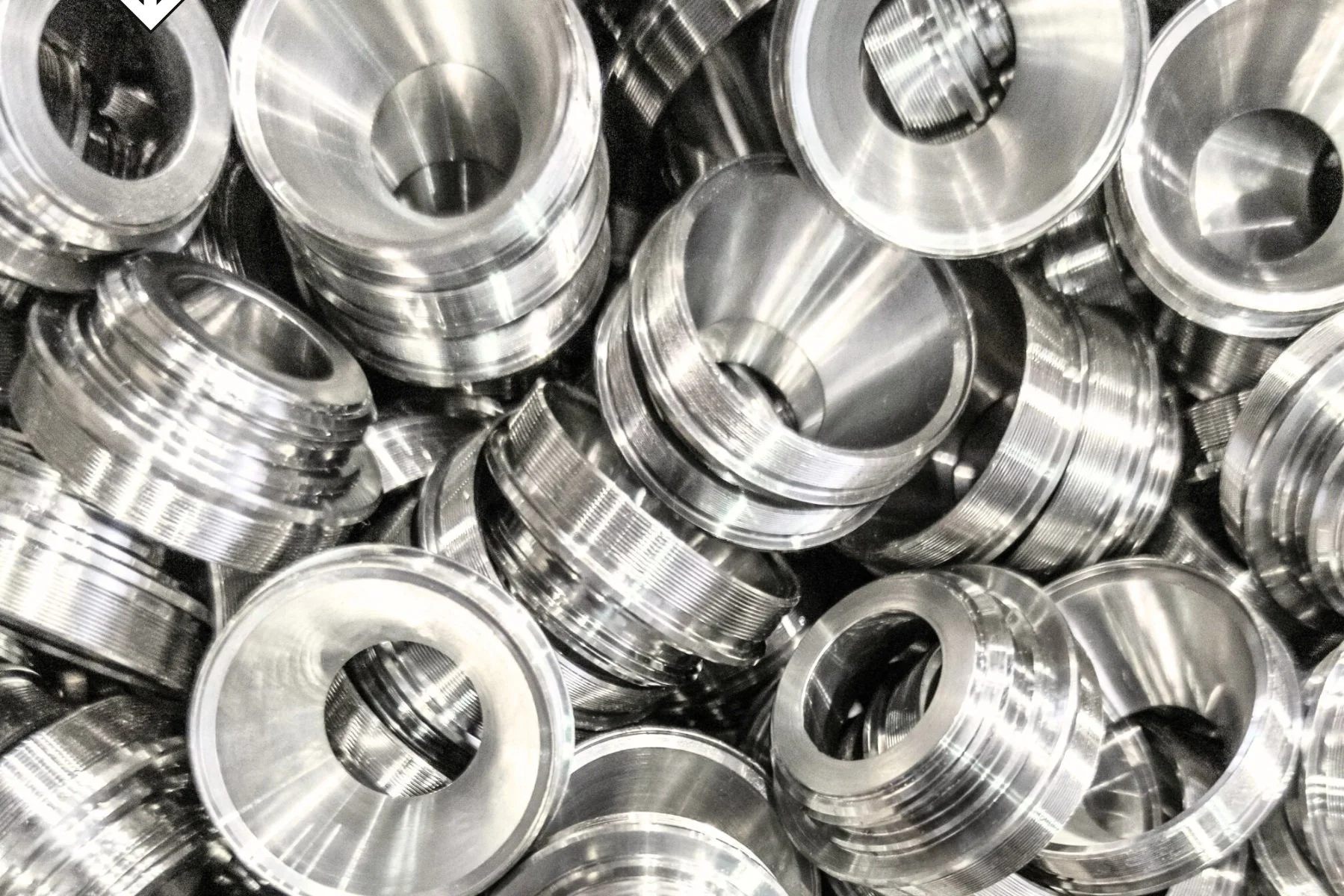

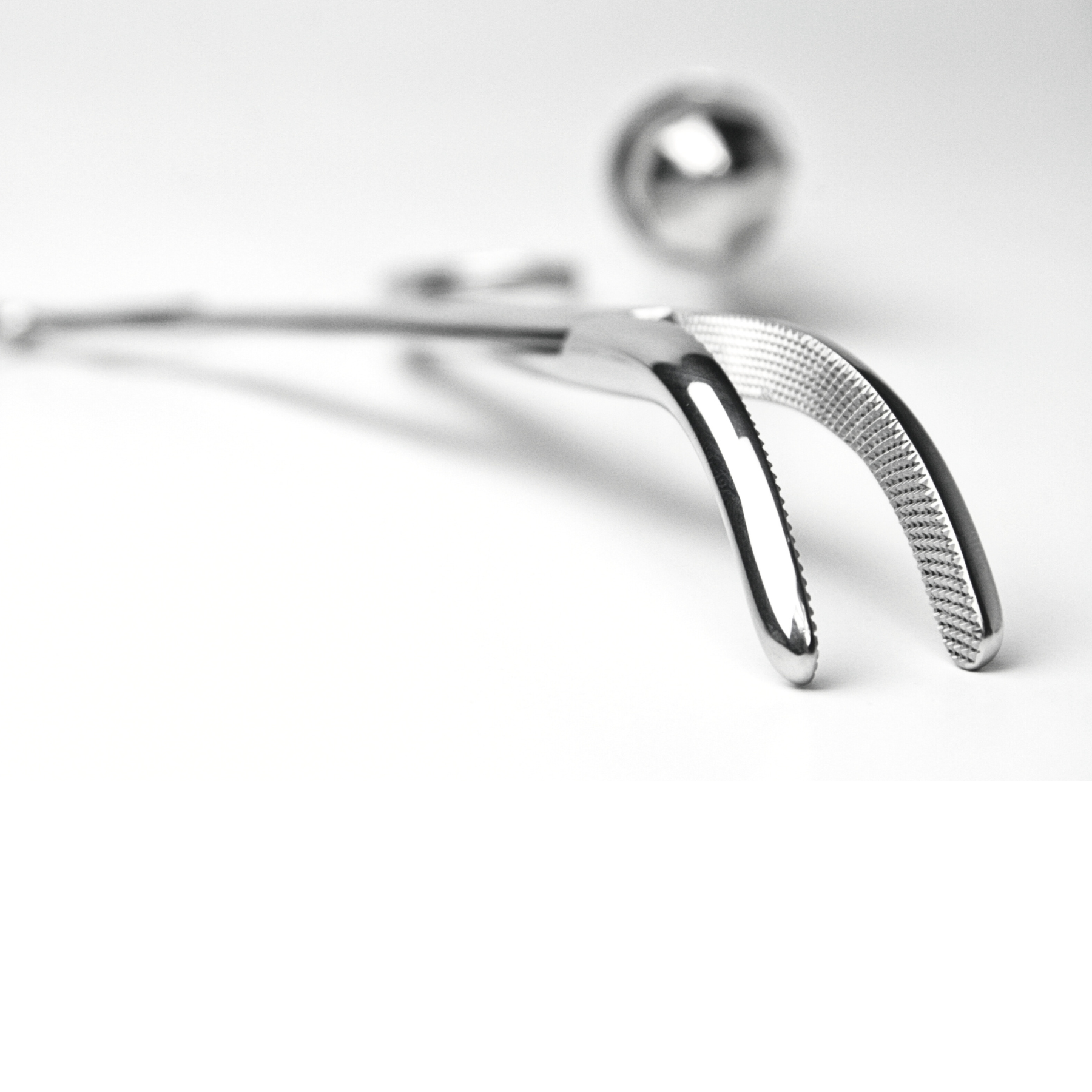

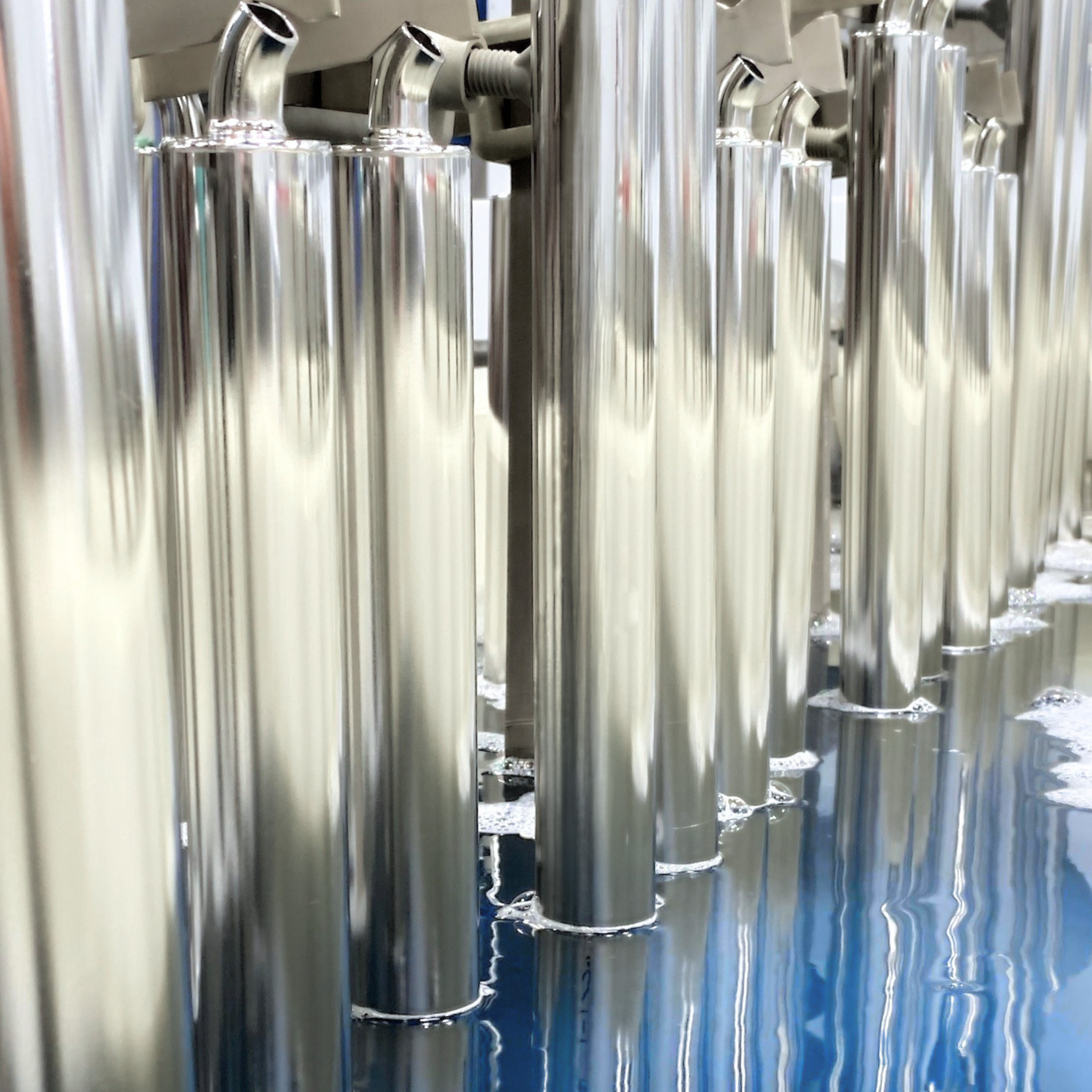

CLA (N)
1
2
4
8
16
32
53
125
250
500
1000
2000
SURFACE ROUGHNESS CONVERSION CHART
Ra (micrometers)
0.025
0.05
.1
.2
0.4
0.8
1.6
3.2
6.3
12.5
25.0
50.0
Ra (microinches)
1
2
4
8
1.6
32
63
125
250
500
1000
2000
RMS
1.1
2.2
4.4
8.8
17.6
32.5
64.3
137.5
275
550
1100
2200
Ra = Roughness Average in micrometers or microinches.
RMS = Root Mean Square in microinches.
CLA = Center Line Average in microinches.
Rt = Roughness Total in microns
N = New ISO (grade) scale numbers.
Cut-off Length = Length required for sample.
Rt
0.3
0.5
0.8
1.2
2.0
4.0
8.0
13
25
50
100
200
N
1
2
3
4
5
6
7
8
9
10
11
12
Cut-off Length (in)
0.003
0.01
0.01
0.01
0.01
0.03
0.03
0.1
0.1
0.1
0.3
0.3
Cut-off Length (mm)
0.08
0.25
0.25
0.25
0.25
0.8
0.8
2.5
2.5
2.5
8.0
8.0
ELECTROPOLISHING SPECIFICATIONS
ASTM B912-02
1.1 This specification covers the passivation of stainless steel alloys in the 200 (UNS2XXXX), 300 (UNS3XXXX), and 400 (UNS4XXXX) series, and the precipitation-hardened alloys, using electropolishing procedures
6. Test Procedures 6.1 Water Immersion Test (Specification A967/A967M)— The article(s) shall be alternately immersed in distilled water for 1 h, then allowed to dry for 1 h for twelve wet-dry cycles (24 h total). Failure is indicated by the presence of red rust or staining as a result of the presence of free iron on the surface.
6.2 Humidity Test (Practice A380/A380M, Specification A967/A967M)—The article(s) shall be subjected to 100 % humidity at 38 6 2°C in a suitable humidity cabinet for a period of 24 h. Failure is indicated by the presence of red rust or staining as a result of the presence of free iron on the surface.
6.3 Salt Spray (Fog) Testing (Practice B117 (ISO 9227))— The article(s) shall be subjected to the prescribed test for a minimum of 2 h in an accredited cabinet. Failure is indicated by the presence of red rust or staining as a result of the presence of free iron on the surface.
6.4 Copper Sulfate Test (Practice A380/A380M, Specification A967/A967M)—See Appendix X2. The article is swabbed with an acidified solution of copper sulfate. Failure is indicated by the presence of a copper-colored deposit or copper-colored spots, or both. This test is not to be used on martensitic 400 series stainless steels.
ES2005 Rev A (Parker Hanifin Quick Coupler Division)
2.3 The Electropolish process in this spec shall be primarily used to improve appearance and corrosion resistance. 2.4 Unless otherwise specified on the drawing, the material removal shall be .0002" to .0004".
3.1 Parts to be electropolished shall be cleaned by any method that leaves the parts free of oil, grease, rust, scale or other foreign matter without adversely affecting the base material. 3.2 Electropolishing may be accomplished by any applicable process provided the finished product meets the requirements of this spec. 3.3 An electropolished parts shall have a smooth, high lustre, uniformly bright surface, free of surface contamination, residual solution and solution stain. 3.4 An electropolished part shall be capable of meeting the applicable quality assurance provision of QQ-P-35C (superseded by ASTM A967-17).
ASTM A967-17 Testing Methods we offer-13.3.1 Practice A—Water Immersion Test (see 14.1), 13.3.2 Practice B—High Humidity Test (see 14.2), 13.3.3 Practice C—Salt Spray Test (see 14.3), 13.3.4 Practice D—Copper Sulfate Test (see 14.4)
FAQs
-
The reverse plating process often called “electropolishing” is also referred to as electrochemical polishing, anodic polishing, electrolytic polishing, or EP.
-
The electropolishing process involves an electrical current passing through stainless steel or alloy parts submerged in a sulfuric or phosphoric acid bath mixture to remove a thin metal surface layer.
-
Electropolishing may not be suitable for components with intricate internal passages, as the process primarily affects external surfaces. It may also not be suitable for all metals and alloys, so a feasibility study is recommended.
-
Electropolishing is effective for a wide range of Stainless-Steel metal components, but its suitability depends on factors such as the geometry, size, and material of the part. It’s best to consult with our electropolishing experts at Arrow for specific recommendations.