Automated Shot blasting
with steel & Stainless Steel
WHAT IS SHOT BLASTING?
Our Shot Blasting that involves propelling steel or stainless steel shot at high velocity to clean, strengthen, or polish a surface. The process is ideal for removing rust, scale, or coatings, and preparing surfaces for subsequent treatments.
Available in both automated and non-automated setups. Automated machines handle larger batches for increased efficiency, while non-automated machines allow for specialized or lower-volume work.
-
Thorough Surface Cleaning: Effectively removes rust, scale, old coatings, and surface contaminants.
Enhanced Surface Preparation: Creates an even, textured surface that improves adhesion for coatings and treatments.
Increased Durability: Strengthens the surface by hardening the outer layer, enhancing wear resistance.
Consistent Surface Finish: Provides a uniform finish, crucial for parts needing an even aesthetic or consistent coating application.
Cost-Effective Preparation: Reduces the need for manual cleaning and extends the lifespan of subsequent coatings.
-
Loading: Parts are placed into the blasting chamber, which can be automated or manually operated based on part size and volume.
Media Propulsion: Steel or stainless steel shot is propelled at high velocity using a turbine or air pressure system.
Impact and Cleaning: The media impacts the surface, removing unwanted contaminants and creating a uniform texture.
Inspection: Parts are checked for cleanliness and uniformity before moving on to the next step in production.
-
Automotive: For cleaning and preparing vehicle components like engine parts and chassis before coating or assembly.
Aerospace: To prep parts that must meet stringent durability and cleanliness standards.
Construction: Structural steel elements and heavy machinery components often need surface preparation before painting or coating.
Manufacturing: For prepping metal parts that will undergo further processing or coating.
Medical Devices: Ensures clean, textured surfaces that can meet stringent safety and adherence standards.
Military and Defense: Prepares parts for protective coatings and enhances their durability.
-
Cerakote: Prepares the surface to ensure strong adhesion and optimal coating performance.
Anodizing: Prepares the surface to promote uniform color and finish.
Powder Coating: Creates a textured surface that allows powder coatings to bond effectively.
Other Treatments: Works well for prepping parts that need bonding or adhesive applications.
-
Steel and Stainless Steel Components: Structural parts, machine frames, and heavy-duty fittings.
Cast Iron Parts: Such as engine blocks and large gears.
Aluminum Parts: Prepped for coatings or further processing like anodizing.
Welded Assemblies: To clean welds and prep for painting or coating.
Pipes and Tubes: To remove scale and prep for coatings or insulation.
Industrial Equipment: Parts like pumps, valves, and housings that need uniform surfaces before finishing treatments.
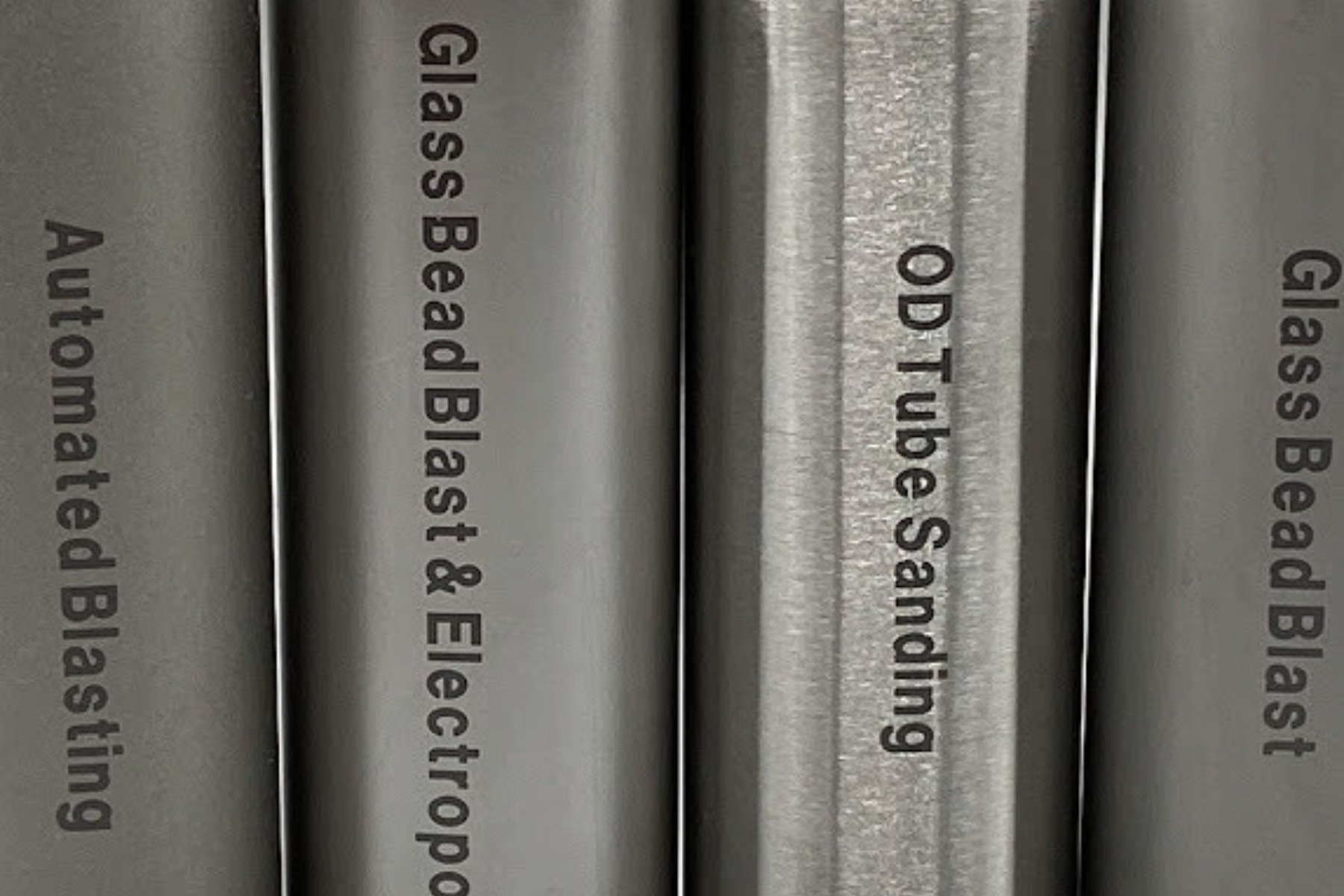
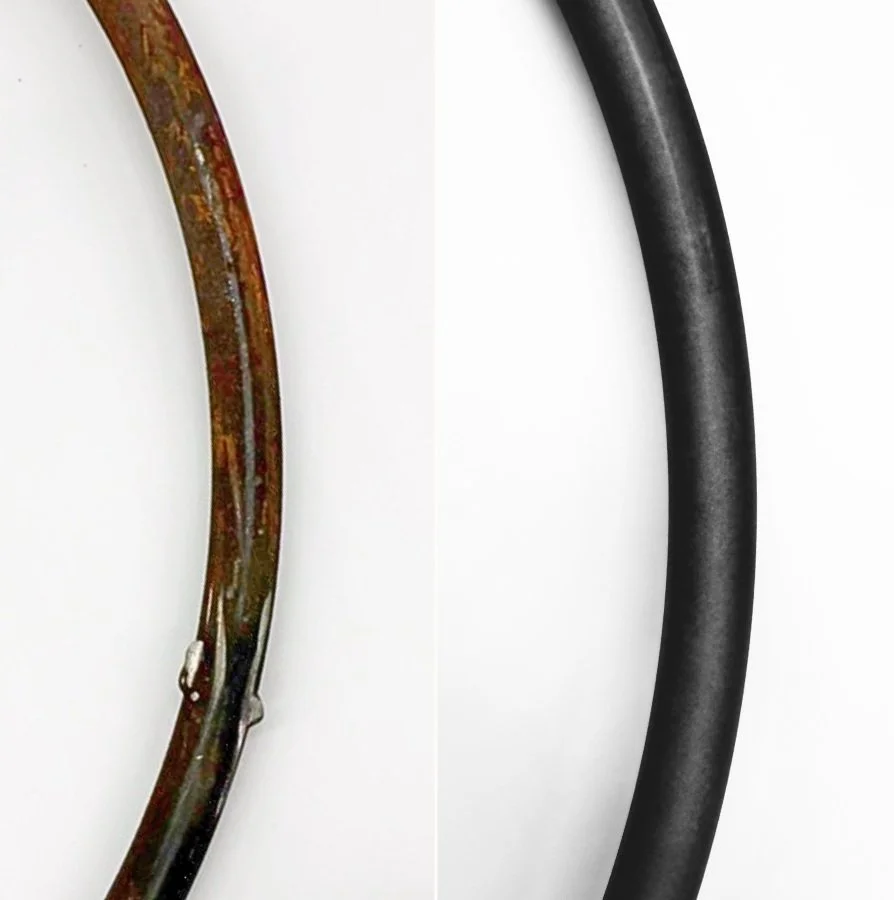
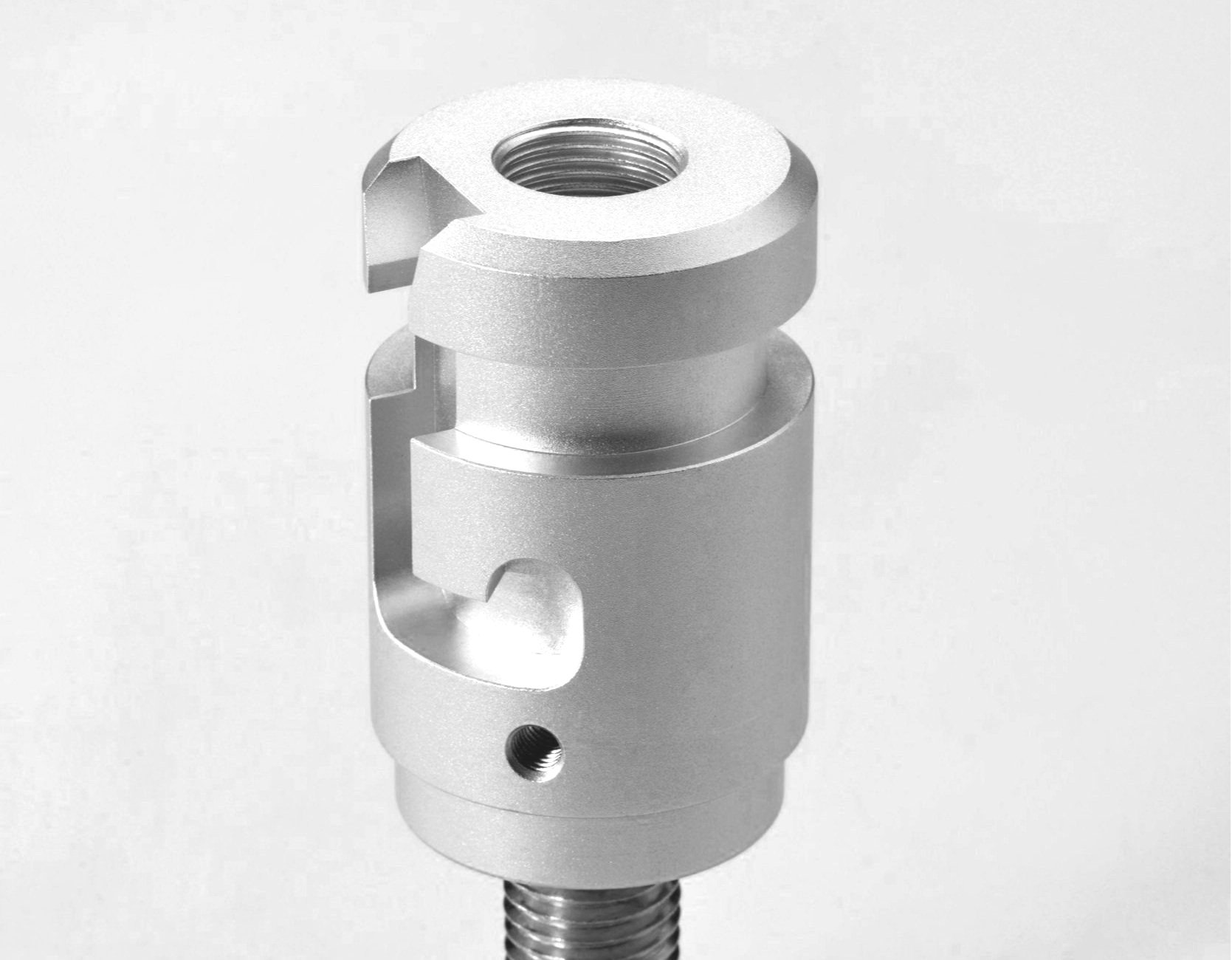



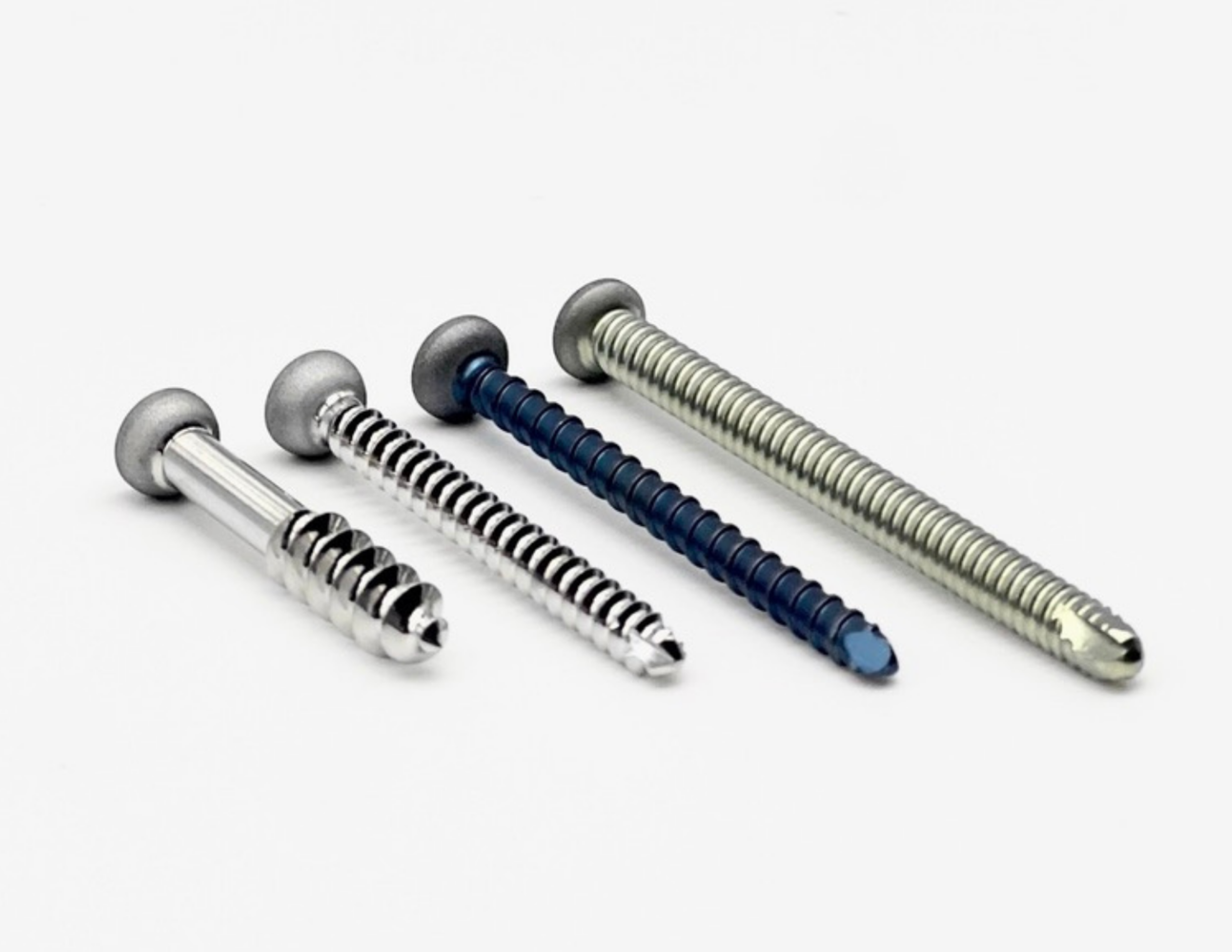
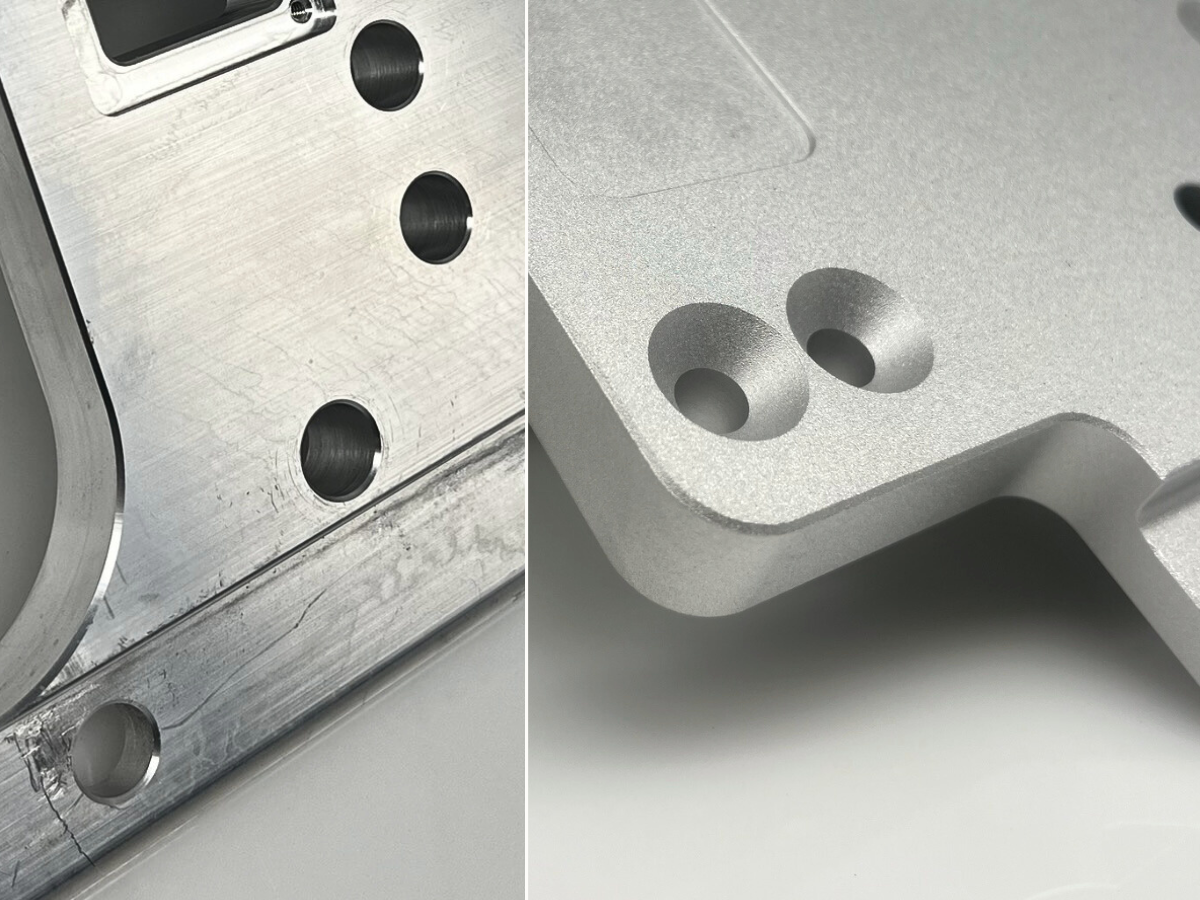