PRECISION QUALITY ABRASIVE GRIT BLASTING SOLUTIONS
Abrasive grit blasting is a surface finishing process where a high-pressure stream of abrasive particles is propelled against a surface to clean, smooth, roughen, or shape it. This method is widely used in various industries for tasks like surface preparation before coating, paint removal, rust removal, and improving surface texture. Various abrasive medias include: Glass Bead, Aluminum Oxide, Steel Grit
WHAT IS ABRASIVE GRIT BLASTING?
-
The abrasive grit blasting process ensures efficient surface preparation or finishing:
1. Preparation
Surface Assessment: Inspect the material or part to identify areas needing treatment and determine the appropriate abrasive and pressure settings.
Masking or Protection: Cover areas that do not require blasting with protective tape, masks, or shields to prevent unintended damage.
Safety Setup: Operators wear safety gear, including gloves, goggles, helmets, and respirators. The blasting area is often enclosed or contained to prevent dust and debris from spreading.
2. Abrasive Selection
The type of abrasive is chosen based on the material being blasted and the desired result. For example:
Aluminum Oxide: For aggressive cleaning or surface profiling.
Glass Beads: For a smooth, polished finish.
Steel Grit: For heavy-duty rust and scale removal.
3. Blasting Process
Application: The operator directs the high-pressure stream of abrasive particles onto the surface using a nozzle.
Technique: Maintain a consistent distance (typically 6–12 inches) from the surface. Move the nozzle in smooth, overlapping strokes to ensure even coverage.
Pressure Adjustment: Adjust pressure based on the surface material and the level of finish required.
This streamlined process ensures a precise and high-quality finish, tailored to the specific requirements of the project.
-
Abrasive Material: The "grit" refers to the abrasive particles used, which can include materials like aluminum oxide, glass beads, steel grit, or silica sand, depending on the desired result.
Equipment: The process uses a blasting machine with a nozzle that directs the abrasive particles at high velocity.
Surface Preparation: It is ideal for removing contaminants like dirt, rust, old coatings, and mill scale, creating a clean and properly textured surface for subsequent treatments like painting, coating, or anodizing.
Versatility: Grit blasting can be customized to achieve various levels of roughness or smoothness based on the type of abrasive and pressure settings.
-
Enhances the adhesion of coatings or paints.
Improves the durability of treated surfaces.
Provides a uniform finish on complex or irregular shapes.
-
Abrasive grit blasting is a versatile surface finishing process used across various industries. Here are some typical applications and parts that benefit from this service:
1. Aerospace Industry
Applications:
Surface preparation for coatings like anodizing or painting.
Removal of oxidation, corrosion, or old coatings.
Improving surface texture for better adhesion.
Parts:
Aircraft fuselage components.
Turbine blades and engine parts.
Landing gear components.
2. Automotive Industry
Applications:
Cleaning metal surfaces before painting or powder coating.
Removing rust, grease, or scale from parts.
Enhancing the texture of surfaces for decorative finishes.
Parts:
Engine blocks and cylinder heads.
Suspension components.
Wheels and chassis parts.
3. Medical Industry
Applications:
Creating micro-roughened surfaces for implants to improve osseointegration.
Cleaning and prepping parts for coatings like titanium or ceramic.
Parts:
Orthopedic implants (e.g., knee and hip joints).
Surgical instruments.
Medical device housings.
4. Military and Defense
Applications:
Prepping surfaces for corrosion-resistant coatings.
Stripping old paint or coatings without damaging the substrate.
Parts:
Firearms and weaponry components.
Military vehicles and tanks.
Ammunition casings.
5. Industrial and Manufacturing
Applications:
Prepping parts for welding, painting, or coating.
Removing surface contaminants like grease or scaling.
Restoring worn or corroded components.
Parts:
Tools and dies.
Machinery housings.
Pipes and valves.
6. Construction and Infrastructure
Applications:
Prepping steel beams and structures for protective coatings.
Cleaning and restoring concrete or stone surfaces.
Parts:
Steel bridges and frames.
Concrete walls and floors.
Structural supports and rebar.
7. Firearms and Sporting Goods
Applications:
Preparing surfaces for finishes like Cerakote or anodizing.
Stripping and refurbishing old coatings.
Parts:
Gun barrels and receivers.
Archery equipment.
Bicycle frames and components.
8. Marine Industry
Applications:
Removing barnacles, rust, and old paint from ship hulls.
Prepping surfaces for anti-corrosion coatings.
Parts:
Boat hulls and propellers.
Offshore platform components.
Marine pipelines and tanks.
9. Energy Sector
Applications:
Prepping parts for heat-resistant or anti-corrosion coatings.
Cleaning turbine and generator components.
Parts:
Wind turbine blades.
Oil and gas pipeline components.
Power plant equipment.
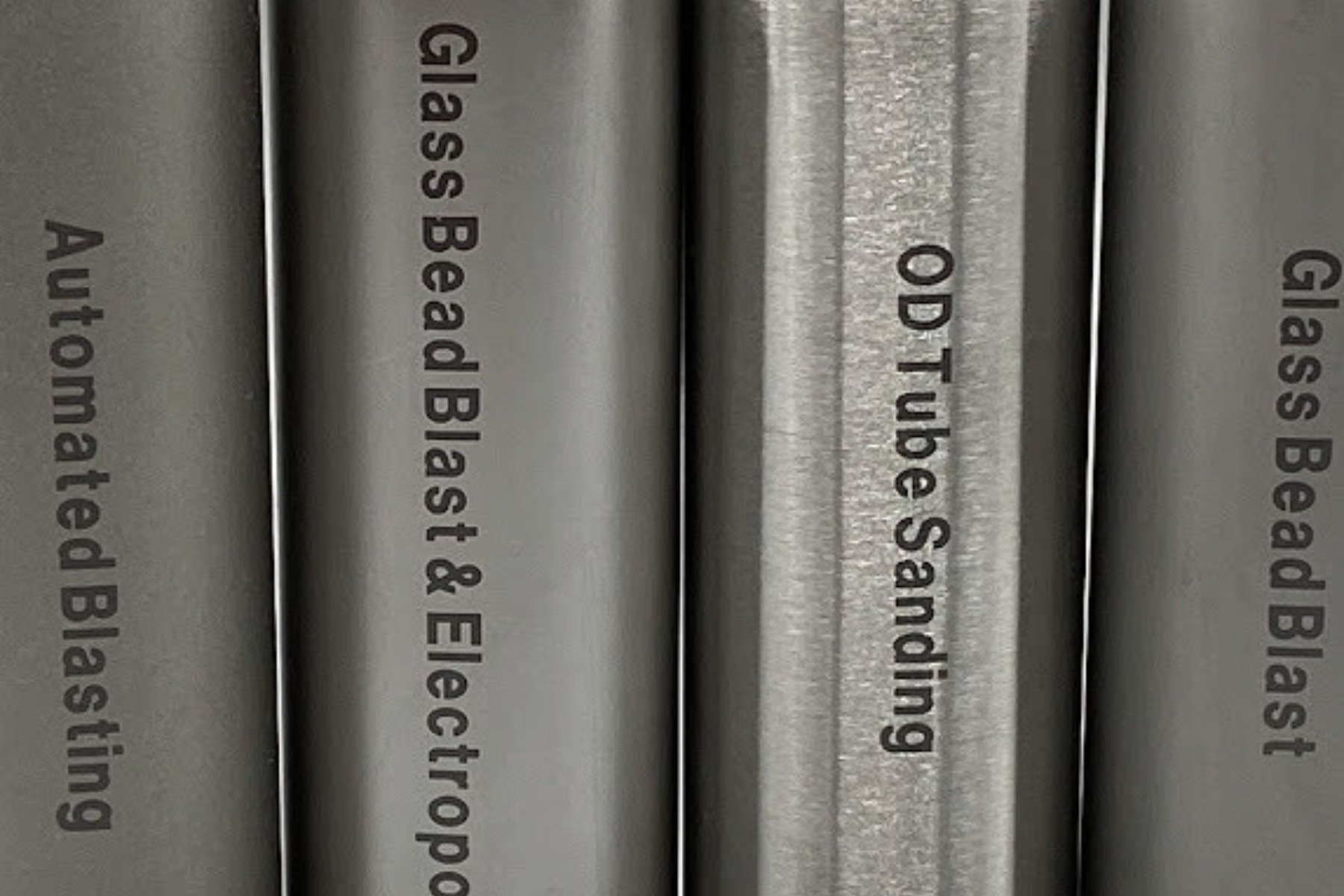
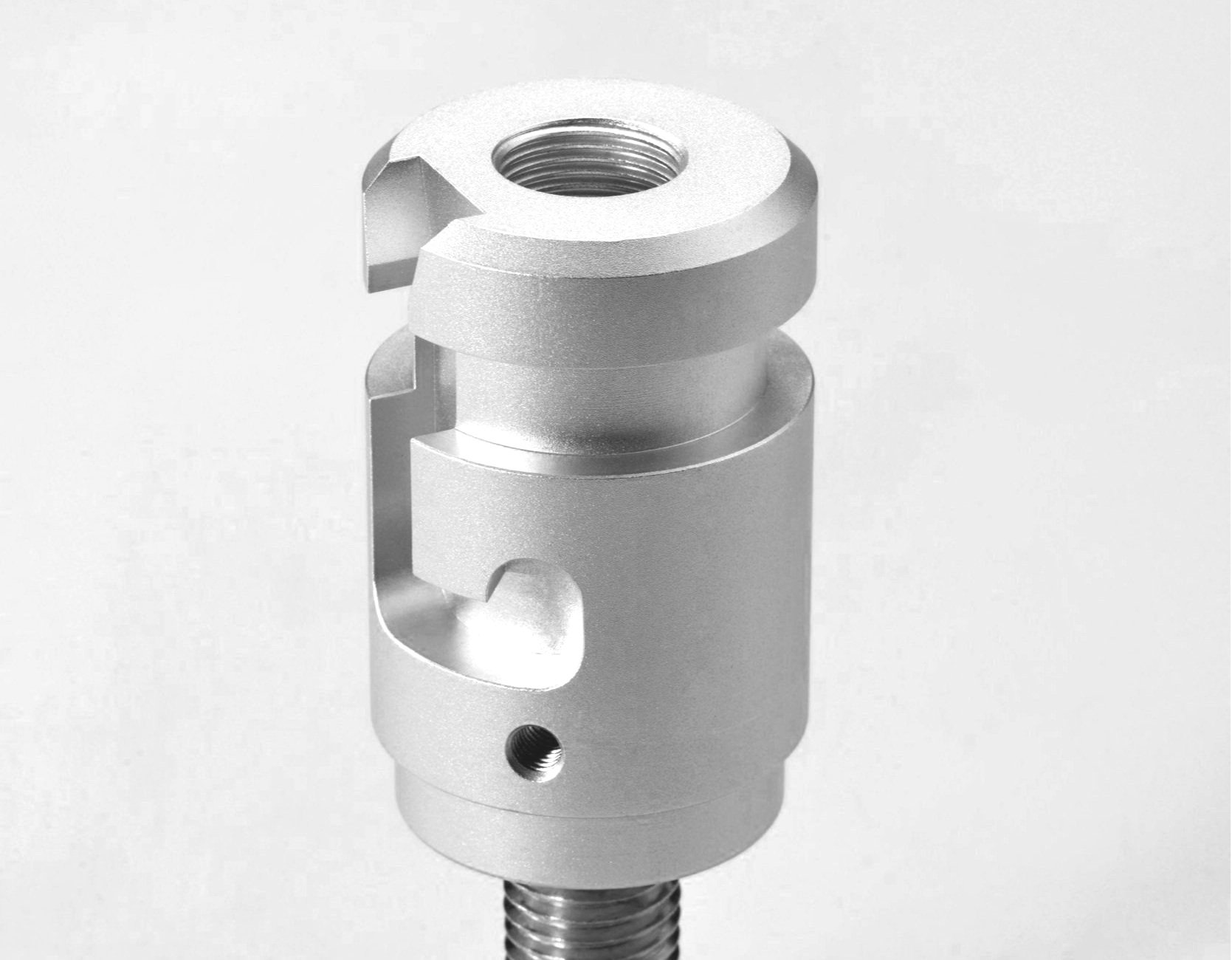

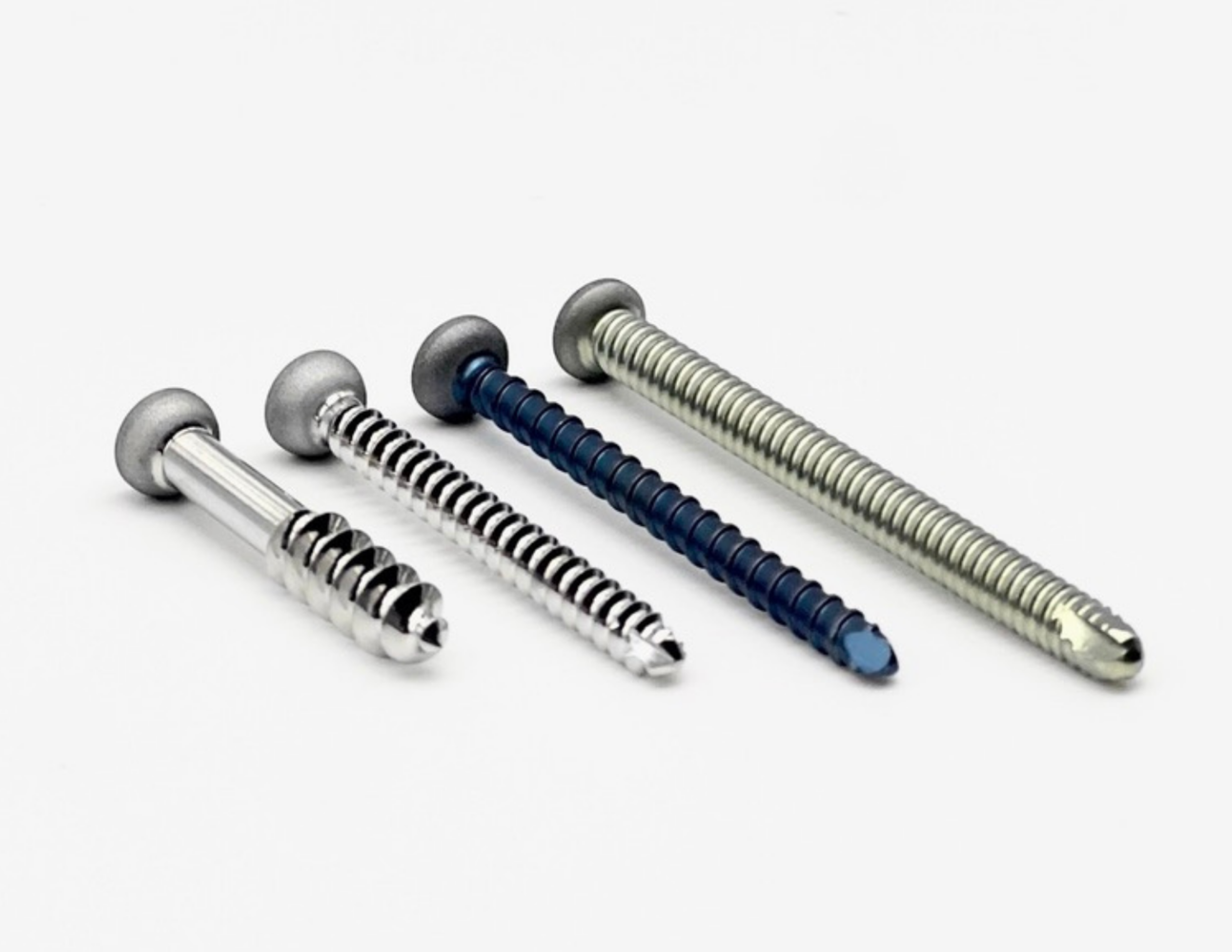


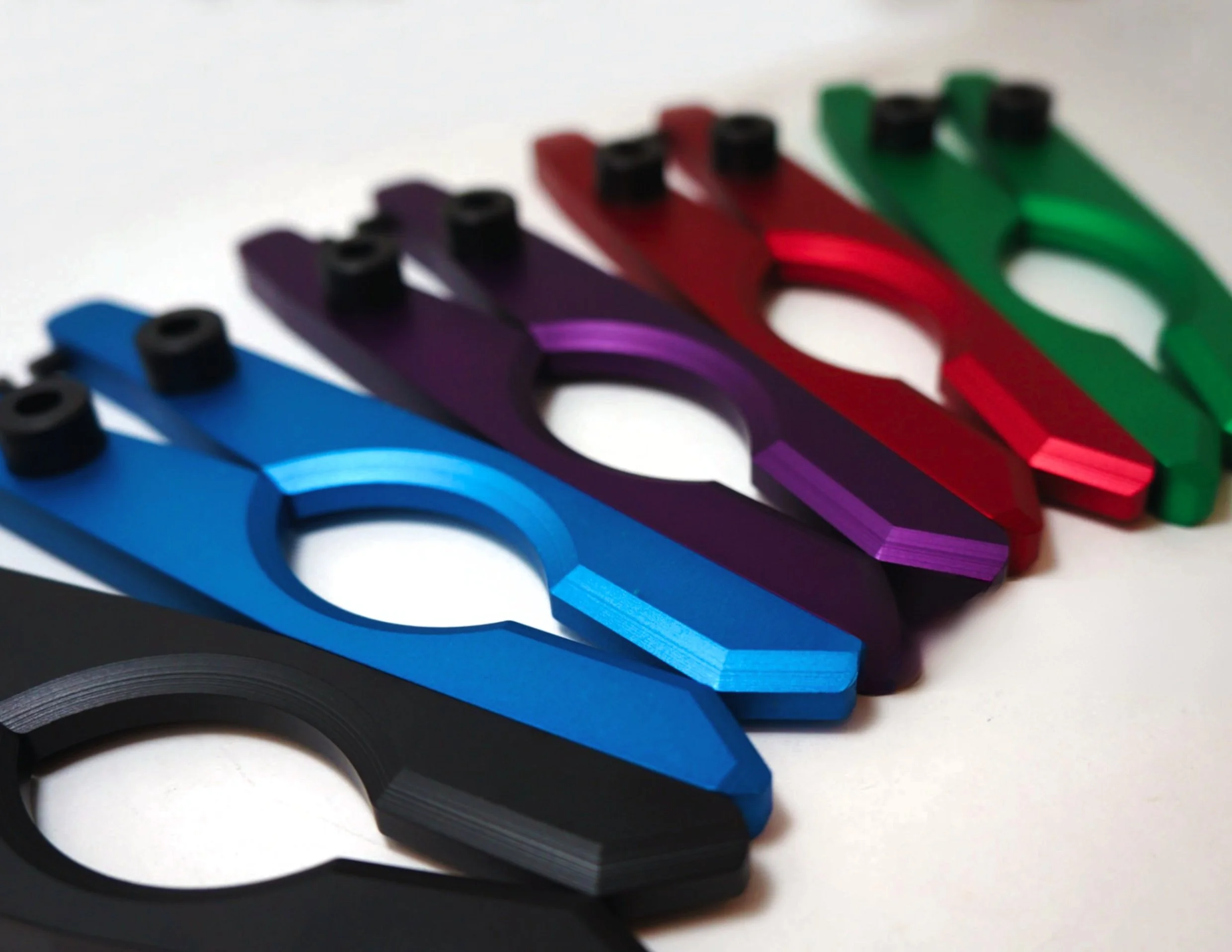

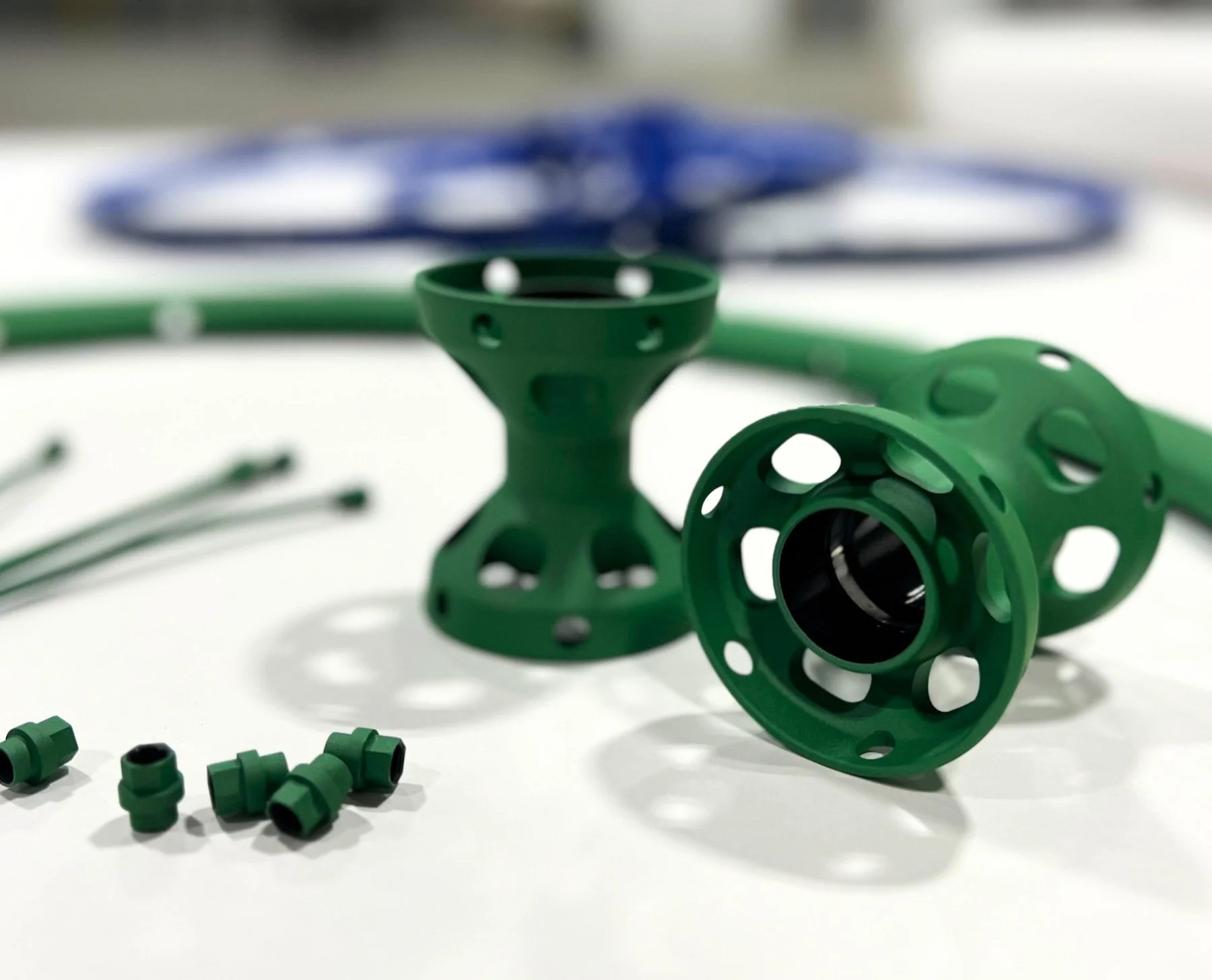
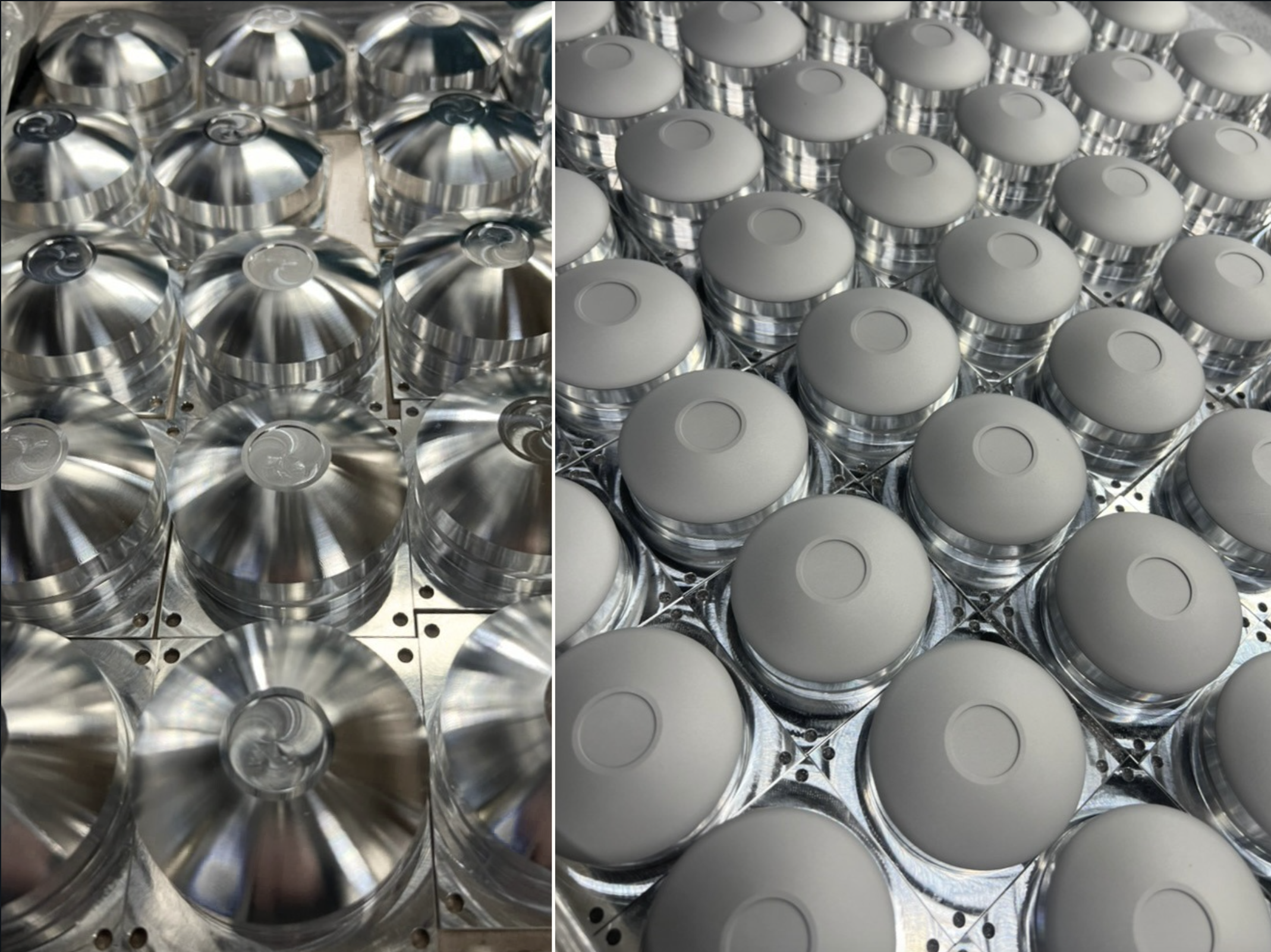